Two productive days! Yesterday I had my first large rivet session. I riveted the stiffeners to the rudder skin. Backriveting is the best option here, so the first step is to insert rivets in the holes and fix them with tape. I use Scotch Magic Tape -- much cheaper than rivet tape and works just as good.
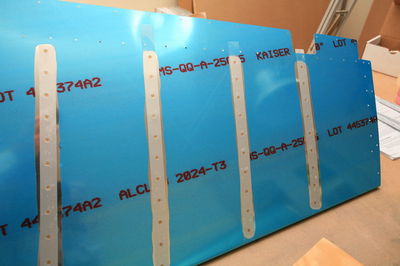
Then you place the skins with the manufactured rivet heads down on a heavy flat chunk of steel and form the shop heads with the rivet gun. This is how the skin looked afterwards; it really is a different beast now, gone is all the floppiness:
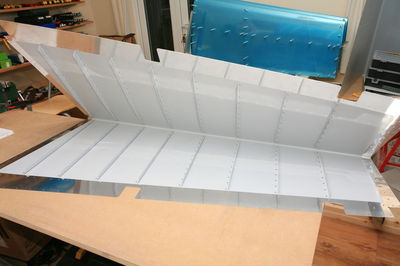
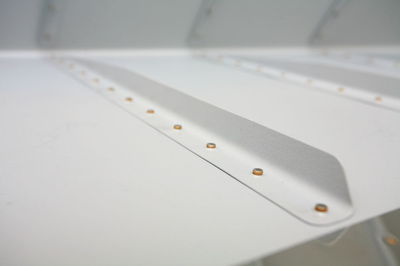
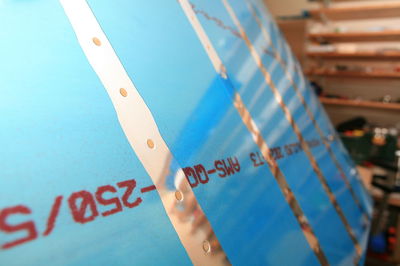
Then I assembled the VS rear spar. Ready for riveting:
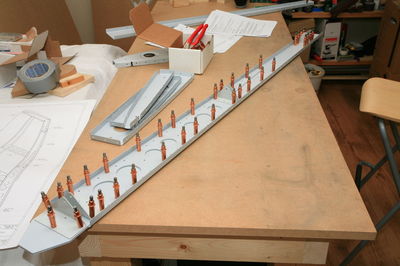
I taped over the holes where the ribs will be attached, so that I don't accidentally put rivets in:

All done, gotta love that pneumatic squeezer!
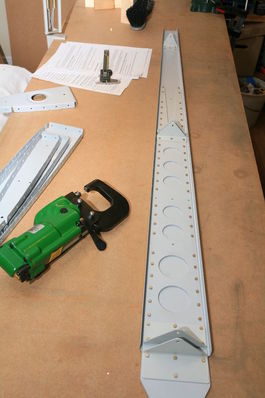
In the lower part of the spar flush rivets are used. That's where the VS will be attached to the fuselage, and universal rivet heads would interfere:
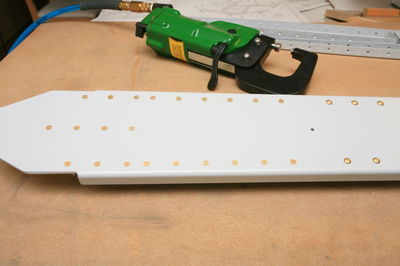
This afternoon I first riveted the VS ribs to the front spar:
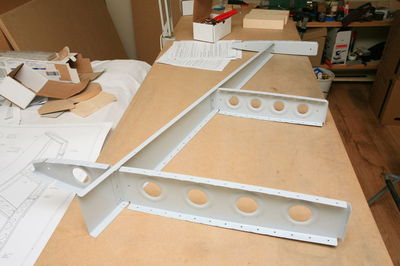
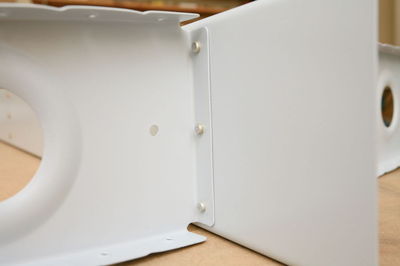
I told you that I got some runs on the first ribs I primes ...
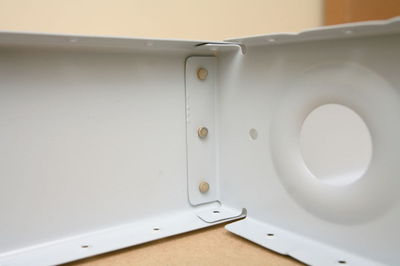
Now I could cleco and then rivet the VS skin to the front spar and the ribs. I love that tungsten bar!!!
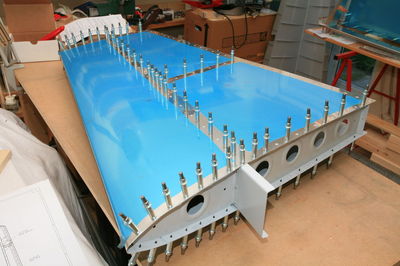
I drilled out four rivets on the VS. On two I slipped with the bucking bar (see the picture below) and two were simply too short. Van's calls for AN426AD3-4 rivets where the front spar and the main rib at the bottom meet, but there's no way to get a proper shop head with that. I ended up using -4.5 and that worked fine.
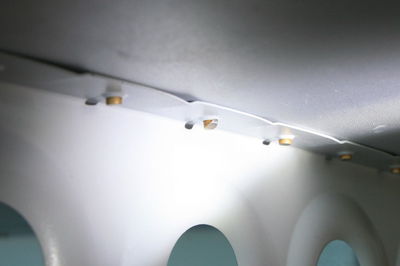
Look ma, no clecos! (Except on the rear spar, that is. I can't close any parts before someone official has looked at them.)
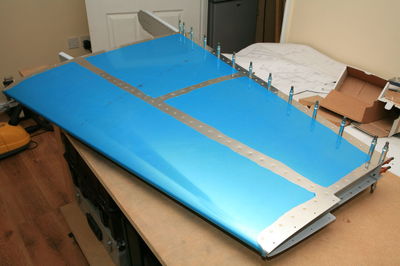
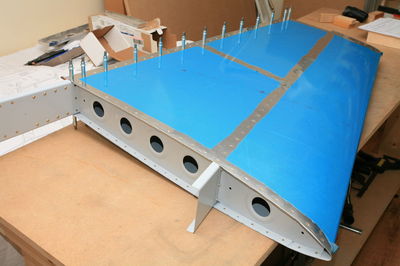