The past few weeks were dominated by work, work, and ... work. I haven't been home a lot, and the little time I was here I spent either at the computer or sleeping. Okay, that's not entirely true. I did actually take a long weekend off beginning of October (wow, that's long ago) to go to Milfield with a small group of people from my glider club. The aim was to fly in the wave, and I did three times.

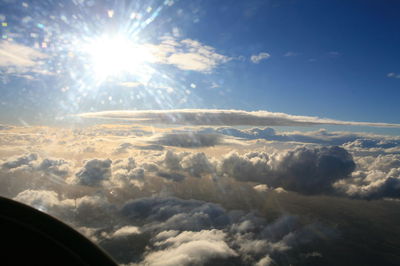
Some fun with a mini-cumulus -- does this count as self-portrait?
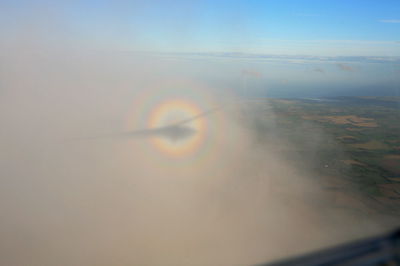
Fast forward to today's afternoon. Work finally got a bit calmer (it will change again, but that's another story) and I took advantage of it and got into the workshop. Van's calendar on the wall still showed the September picture, so I flipped two pages and started to work.
I got the frame for my DRDT-2 welded, but they bolted the die holder on the wrong way. So I fixed that and adjusted everything. What a nice tool! I also got a backriveting plate, so I can now return Steve's tools.
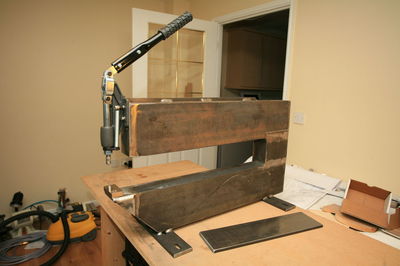
Then I match-drilled the R-716 rudder bottom attachment strips to the rudder, and drilled all the remaining holes to final size.
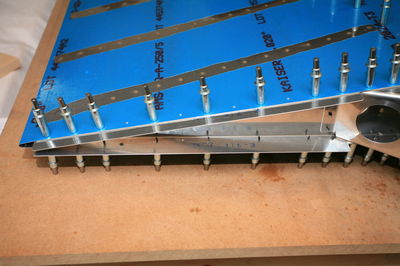
Not a long session today, but it's good to be back on the project. The wings should arrive before Christmas; we hope to beat the VAT increase deadline. They are already in the container.